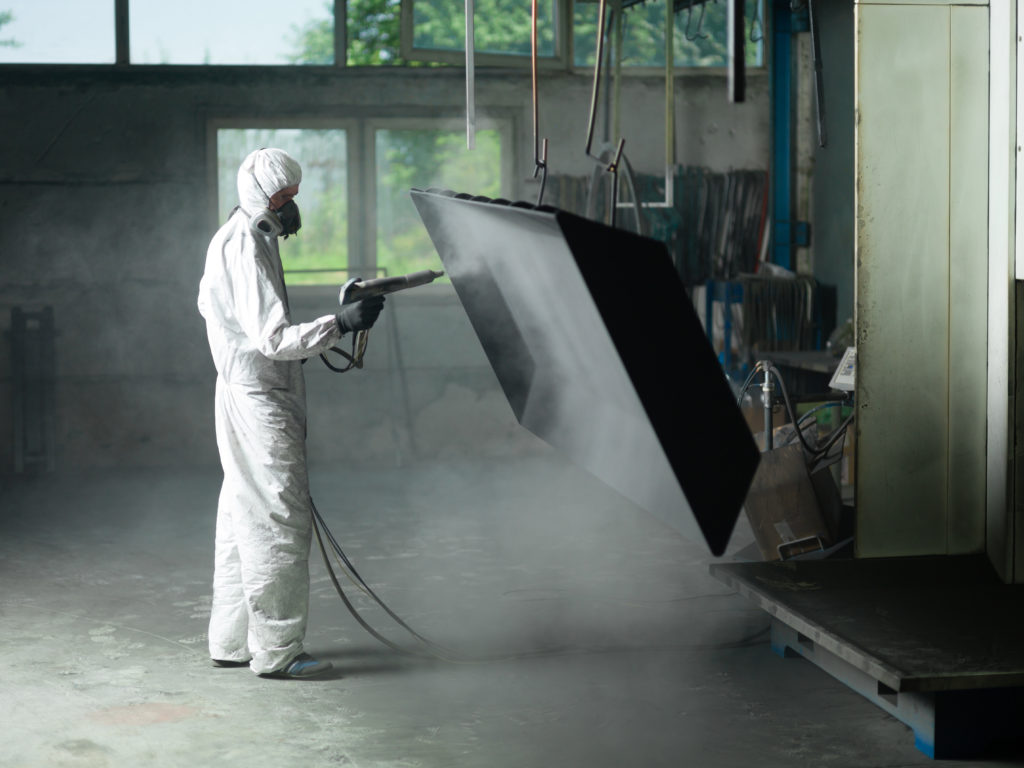
Founded in 1997, Fireblast Global started specializing in the design and production of fire training equipment. Over the years, our scope expanded, allowing us to offer a wide range of services that include sheet metal services such as precision laser cutting and press brake forms, as well as additional fabrication services including: prototyping, welding, powder coat, galvanize, cerakote, industrial control system design, and engineering services. In this article, we want you to know more about the other facets of our fabrication services.
What Is Sandblasting?
Sandblasting is a process that propels very fine particles of an abrasive material at a high velocity and high pressure to clean or etch a surface. It can be water-driven or air-driven, depending on the surface to be sandblasted. Water-driven sandblasting is most commonly used for brick or concrete surface preparation, where the cooling effect of water reduces surface deterioration. On the other hand, air-driven sandblasting is most used for metal surfaces to prevent moisture build-up and avoid water intrusion into the surface.
A typical sandblasting setup consists of an air compressor, a blaster nozzle, and abrasive material. Aside from sand, some commonly used abrasive materials in this technique are steel grit, copper slag, walnut shells, plastic pellets, and coconut shells. The abrasive particles are known irritants to the eyes, skin, and lungs, so wearing proper safety gear is needed when carrying out sandblasting.
Importance of Sandblasting
Sandblasting is used to smoothen a rough surface, roughen a smooth surface, or shape a surface depending on the abrasive material used. It is a versatile technique used across many industries. It can be found in the manufacturing, construction, oil and gas, marine, petrochemical, and electronics industries, to name a few. It is vital in maintaining parts, machinery, and equipment clean and operational. It is also useful in a variety of renovation projects. With the force and speed of blast media shot at surfaces, scales and other contaminants that build up can be removed while leaving the underlying material intact.
Applications of Sandblasting
Surface Preparation
Sandblasting is often used to prepare surfaces before coating, painting, galvanizing, oiling, sealing, welding, and adhesive bonding. It strips off paint, greases, oils, and dirt from the surface of machinery or metal that might interfere with the adhesion of coatings, adhesives, and sealants to be applied. Furthermore, it creates a sufficiently rough surface profile that allows better mechanical grip of new coatings, paints, and adhesives. In automotive manufacturing and its aftermarket services, car parts undergo sandblasting to improve material properties and extend the life of parts for restoration.
Surface Finishing
Blasting a surface with spherical media such as steel shot, glass beads, and ceramic spheres refines rough edges, creating a surface with a smooth finish. It removes visible, sharp marks produced during machining and grinding processes. First, larger diameter spheres are shot to improve fatigue strength, followed by smaller spheres for refining the surface finish.
Cleaning
Mechanical cleaning or removal of rust, mineral and carbon deposits, scales, and varnish from surfaces is the most common application of sandblasting. During the sandblasting process, the contaminants are removed without damaging the base material. In an aluminum aircraft, old paint is removed without damaging the aluminum base using plastic media. In chemical plants, sandblasting is useful in maintaining the tanks, pipes, valves, and pumps corrosion-free.
Sandblasting is a quick and efficient way of removing rust, oil, and other harmful contaminants from any surface. It can be automated, making it more efficient than other part cleaning equipment such as grinding wheels, rotary files, abrasive flap wheels, and wire brushes, to name a few. It can also be applied to large surfaces at a lower cost because some blast media types are reusable.
To learn more about Fireblast Global, check out our latest blog posts, and feel free to contact us for any inquiries.