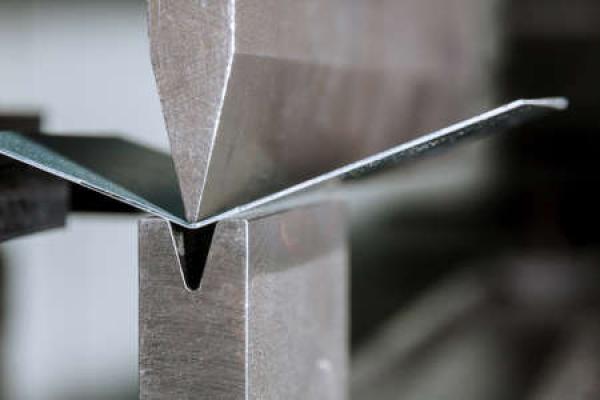
People have bent and shaped metal to create certain tools and other products for centuries. But we’ve come a long way since the old days and a major aspect of that progress has been the adoption of press brake forming. This technique, while not entirely new, has evolved dramatically with advancements in technology, allowing metal fabricators to push the boundaries of precision, efficiency, and versatility. Let’s take a closer look at why press brake forming was such an important step in the world of metal fabrication.
Unmatched Precision and Repeatability
One of the most significant leaps forward with press brake forming is the precision it offers. Traditional metal forming methods often struggled with consistency, especially for complex bends and folds. Press brake forming, enhanced with computer numerical control (CNC) technology, changes all that. CNC press brakes can execute complex bending operations with pinpoint accuracy, down to a fraction of a millimeter.
This precision is crucial not just for the fit and function of parts, but also for their aesthetic. In industries where the finish and form are just as important as the function of the product, the repeatability of CNC press brakes ensure that each part is a carbon copy of the last, maintaining quality and customer satisfaction.
Versatility Across Materials and Designs
What truly sets press brake forming apart is versatility. Modern press brakes can handle anything from stainless steel to aluminum. This versatility extends to thickness and size, with press brakes capable of handling both thin sheets and heavy plates.
The adaptability of press brake set ups, meanwhile, allows for quick changes between jobs. This flexibility is invaluable for custom job shops or industries where production runs vary frequently, allowing them to switch from one product to another without lengthy downtime.
Cost-Effectiveness and Efficiency
Press brake forming stands out for its cost effectiveness and operational efficiency. With advancements in technology, setups are quicker, run times are faster, and material waste is minimized. The ability to bend, fold, and form metal accurately reduces the need for secondary processing, cutting down on additional machining or finishing steps.
Press brake forming is not just another metal fabrication method—it’s a symbol of industrial progress. If you’re intrigued by the possibilities of what press brake forming could add to your projects, Fireblast Global is here to turn that potential into reality. Our expertise and state-of-the-art technology equip us to handle all your metal fabrication needs. Give us a call at 951-277.8319 to get started!